Anatomy of a Proactive Well Servicing Regimen Part 4: Timeline Tracking
- Kalcy Thomas
- Aug 31, 2020
- 4 min read
To ensure your well servicing regimen is running as effective as possible, you need some form of monitoring it. I have developed and utilized a "Well Servicing Tracker" using a simple excel spreadsheet to track progress and provide a means of looking back to see how things are going. The next few parts of the series, dealing with timeline tracking, prioritization, run time to failure, and $$'s, are all derived from this spreadsheet.

example of a "Well Servicing Tracker"
Timeline Tracking
In order to track the amount of time it takes to return a well to production, and determine opportunities to expedite the process, there are many variables which need to be considered. Some important dates to track are:
- when the failure was discovered
- when the repair request was submitted
- when the failure/well review were complete
- when internal & external approvals were achieved
- when a rig was finally stood up
- when the well was repaired and placed back on production.
Failure
Depending on the level of automation you have on your well(s), the failure might be flagged quite quickly when it occurs, or there might be some delay before the operator finds a problem. If you have a pump off controller (POC) on the well and are either monitoring it closely, or have limitations set to flag abnormalities, the failure will be noticed right away. However if you don't have the advantage of automation, the failure is typically not found until lost production is noticed. Then it is up to the operator to find the culprit via well testing, troubleshooting, etc. Once you find the well that is not delivering what it is supposed to, you can follow the troubleshooting steps found on my website.
Repair request
Over the years, I have developed a repair request form, using input from myself, other optimization techs, operators, foreman, and wellsite supervisors. The point of this is to provide as much information as possible regarding the failure, in order to properly diagnose it (see the last blog entry for more.) Once the operator has determined that intervention is required to get the well producing again, he/she will fill out this form as thoroughly as possible and submit to their lead op or foreman for review. Once the lead op / foreman is satisfied that the operator has provided as much info as possible, he passes it along to the intervention group. Depending on the structure of your company, this might be the optimization tech, engineer, well servicing group, etc.
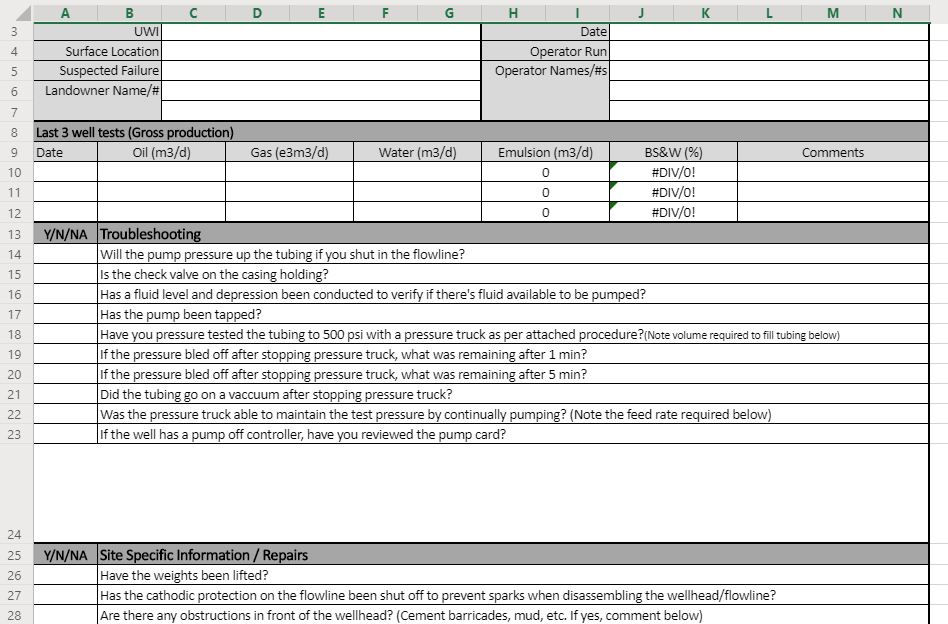
Failure / Well review
The importance of the failure review and the complexity of it was discussed in the last blog entry. This step can definitely take some time, depending on the well files and how readily available information is. Once you have performed a thorough well review, you will want to save that summary of important information to the wellfile to prevent having to do the same thing all over again the next time the well needs intervention.
Internal & External Approvals
Once you have determined how you would like to repair the well and have developed a cost estimate for the entire project, you need to calculate the economics for the proposed workover. If the payout and ROI are favorable, it can be deemed a worthwhile project. Internal approvals are typically easily gained if the project is worthwhile (of course everything depends on commodity pricing and available budgets, which we've learned over the past while...)
However, external approvals can add some complexity to things. Depending on working interests, unitization and operating agreements, partners can sometimes hold up the process. I have spent many hours on the phone and sending emails in the past trying to track down partners in order to get a rapid approval response so we can proceed with workovers, without having to wait for a signed AFE to be returned.
Rig Standing
Once all of the pre-planning for a workover is complete, you have the task of sourcing equipment. If you've been proactive, hopefully you've been in touch with service companies throughout the process giving them a heads up that you'll need equipment. Right now, you shouldn't have to wait too long, but there have been times over the years when oil and gas prices were high, that all of the services were tied up.
Well Repaired & Back on Production
This part of the process ties in with the $$'s section, still to come. If you take longer than planned on a workover, your services will of course cost more than budgetted, and you may be overspent on the project. You can also track which companies are more efficient in completing similar tasks, in order to try and streamline the process and save some money. Hourly rates are typically quite similar from one company to the next, so efficiency and time saved is where you'll save $$.
Conclusion
It is important to dig into each step of the process in order to find inefficiencies. If you find roadblocks, or areas taking longer to complete, you can determine strategies to speed up the process. Getting production back online as quickly as possible is very important, as downtime directly impacts your lifting costs, on a $/boe level. The lower you can keep your lifting costs, the more profitable your company is. And the happier the boss is, the more enjoyable the workplace is.
If you would like to develop a "Well Servicing Tracker" and discuss the important components within, please get in touch.
Thanks, Kalcy
403-391-3758
kalcyhthomas@gmail.com
Comments